Press release, 31st July 2023: £40 million fund launched to unlock 5G benefits across the UK
The top 5 ways 5G boosts the performance of UK manufacturing businesses
March 11, 2024
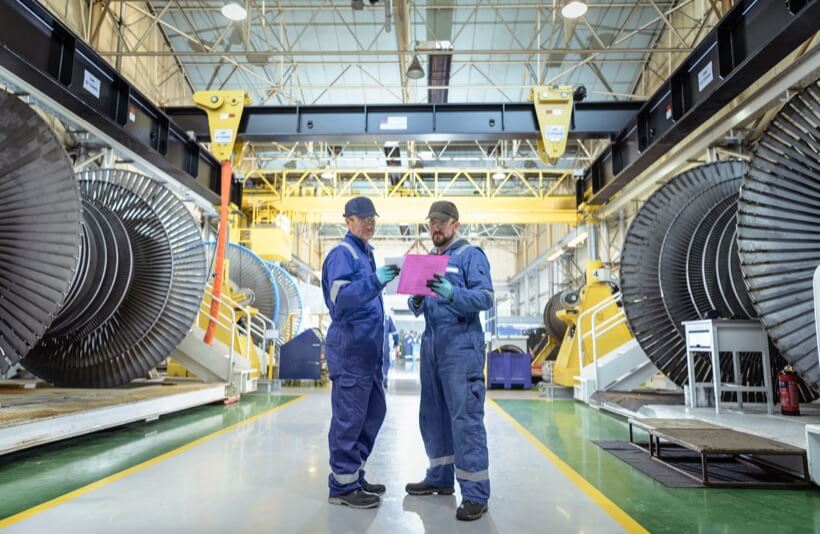
Countdown to business connectivity
From the growing skills gap to complex supply chain issues, manufacturing businesses in the UK currently face numerous challenges.
While there’s no one-size-fits-all solution to these problems, there is one smart way manufacturers can look to boost their business performance – and that’s by exploring the power of better network connectivity.
As it happens, manufacturing is an area ripe for connectivity innovation. Last year, the UK government announced a £40 million fund [1] designed to unlock 5G benefits in the sector.
5G isn’t simply an upgrade of 4G; it’s completely different tech. Up to 100 times faster than 4G [2], with much lower latency, far higher resolution capabilities, enhanced reliability and increased network capacity, 5G makes for excellent comms.
Despite the opportunities on offer, many manufacturing businesses are yet to take advantage – meaning they’re not yet reaping the rewards.
Eager to explore how you can leverage 5G in your manufacturing organisation? Let’s start with some of the more straightforward applications – before counting down to some of the more exciting, future-facing possibilities
5G is up to 100x faster than 4G
5. Real-time collaborative innovation for manufacturing
In the manufacturing world, one of the biggest challenges is cross-function communication. Indeed, effective product development requires that multi-disciplinary teams of designers, engineers and testers work together seamlessly.
5G-powered video calls can facilitate this collaboration. Thanks to its high data speeds, 5G video calls are 4K – four times the number of pixels as a standard 1080p display. On top of this, 5G’s ultra-low latency (the lack of delay between a user’s actions and a system’s response) means participants can perceive the speakers talking in real time – something that can reduce frustration.
With 5G in place, teams can communicate effectively, where they want, when they want. The lag-free experience speeds up everything from product development to innovation and collaboration – making for a stress-free working experience.
5G video calls have
4x the number of pixels
as a standard 1080p display
4. Connected devices for enhanced automation
While factories are already marvels of coordination, 5G really powers up the manufacturing process – paving the way for factories that are as effective and as productive as it’s possible to be.
Thanks to 5G’s near-zero latency, as well as its ability to connect a high number of devices at the same time, factories can replenish their parts and supplies and repurpose robots and tools automatically. Elsewhere, 5G-powered analytics allow for predictive maintenance – reducing downtime to the minimum and boosting productivity.
With 5G as their connectivity bedrock, manufacturers can link machines, sensors, robots and other equipment together. Even better, it doesn’t matter if there are 10 devices to link or 1,000 – 5G has the capacity to support 1 million devices per square kilometre [3].
A number of factories are already reaping the benefits of 5G-powered automation. Working alongside precision parts manufacturer AE Aerospace, FitFactory (an organisation that helps factories with digital transformation) is using 5G to streamline the planning and production process. This involves managing and analysing high-volume data capture, as well as automating manual processes such as logging machine time, measuring parts to specification and inspecting machines
5G has the capacity to support
1 million devices
per square km
3. Real-time remote asset management & monitoring
From industrial robots to assembly lines, 5G-powered sensors can be installed in all kinds of manufacturing assets. These sensors can then transmit data about their performance and supply levels in real time.
Real-time asset data can be a significant benefit to manufacturing, optimising processes, informing production schedules, enabling proactive maintenance and boosting operational efficiency. According to one study, real-time asset data can lead to a 15-25% reduction [4] in the number of defects, amount of waste generated and machine downtime. Even just asset location tracking can boost operational efficiency. Ericsson recently rolled out high-precision indoor tracking, estimating 25% efficiency gains when compared to manual tracking.
Plus, thanks to the ultra-low latency of 5G tech, this data feed will be live or near-live – providing manufacturing professionals with the visibility they need, when they need it
Real-time asset data can lead to an estimated 15% reduction in the number of defects by an estimated [4]
2. Powering up manufacturing training
5G can power highly detailed augmented reality (AR) and virtual reality (VR) experiences. While 5G’s predecessor, 4G, can support AR and VR capabilities to some extent, only 5G has the power to facilitate the high-quality multimedia content necessary for AR and VR applications.
And thanks to 5G’s low latency and faster data speeds, the AR and VR will be responsive and collaborative.In manufacturing,
5G-powered AR and VR can be used for immersive training experiences, which can be harnessed by assembly and maintenance professionals across the board. Effective and exciting, AR and VR training can educate assembly and maintenance professionals faster and reduce downtime. And thanks to its ability to connect to a large number of devices at the same time, the AR and VR training can be truly interactive, with a number of professionals interacting in the same virtual learning landscape at the same time.
Elsewhere, AR and VR can be leveraged at the product design stage. Specifically, product developers can use AR to overlay digital 3D models onto physical objects, aiding in the visualisation process. And on the production line, VR headsets can be used to help technicians better detect defects in products and ensure all items are up to scratch.
1. Digital twins for precision analysis
Only 5G has the capacity to support the sheer quantity of data required for digital twinning – a practice that’s set to revolutionise the manufacturing process.
Serving as a bridge between physical and virtual worlds, 5G-powered digital twins are highly accurate simulations of the production process. Manufacturing professionals can use these simulations to spot anomalies and problems before they happen – informing the predictive maintenance schedules of systems, products and machines. On top of this, they can leverage digital twins to refine designs and optimise processes for quality and efficiency.
Once put in place, manufacturers won’t look back. Digital twins are a significant time and money-saving practice. According to one study, digital twinning can lead to a 15-20% [5] machine utilisation improvement. With this in mind, it’s little wonder why the global digital manufacturing market is expected to hit $1.37 trillion [6] by 2030.
A 5G-powered future from Three Business
The 5G-powered factory is a sight to behold. With unparalleled seamlessness and ultimate connectivity, 5G factories are optimised and innovative. While some of the tech might sound futuristic, many use cases are available here and now.
Three Business is the UK’s Fastest 5G Network [7], providing unlimited 5G power to over 500,000 business customers up and down the country. With flexible contracts and plans, our dedicated team of advisors are at hand – ready to boost your connectivity, streamline your comms and unlock your business’ potential.
Learn more about how we can boost your connectivity, streamline your comms and unlock your team’s potential.